Encoders are particularly suitable for precise position determination in industrial automation. SICK encoders reliably measure rpm, speed, and acceleration. High-resolution optical encoders and extremely rugged magnetic encoders complement one another perfectly and permit exact measurements in complex applications. The measuring tasks are generally split into rotary or linear. While rotary encoders measure rotational movements, linear encoders control, for example, the position or the synchronization in linear movements. Rotary encoders are available as incremental and absolute encoders. Wire draw encoders and linear encoders with a measuring element are available in linear measuring technology. The product range also includes inclination sensors that enable non-contact detection of angles in one or two axes.
Incremental encoder
Incremental encoders generate information about position, angle, and rotation counts. This information is defined by the number of pulses per rotation, which the encoder transmits to the control unit for each rotation. The current position can be determined by the control unit by counting these pulses. Thanks to their versatility, incremental encoders can be perfectly adjusted to applications in factory, logistics, and process automation. Incremental encoders provide, for example, information about the direction of travel and speed of automated guided vehicle systems. The encoder can either be directly mounted on the motor, or mounted on an axle or revolving wheel.
Absolute encoders
Absolute encoders record the rotational movement of the shaft in type-specific angle steps. For this, a unique code pattern is assigned to each angle increment. The number of code patterns available per revolution determines the resolution. Each code pattern forms a unique reference, and therefore transmits an absolute position. Depending on the interface, additional information, such as speed or diagnostic data, can also be transmitted. Absolute encoders are used for absolute recording in a horizontally or vertically executed rotational movement in factory or logistics automation – and much more. Absolute encoders determine the accurate position of the gripper in palletizer systems, as an example.
Safety encoder
In conjunction with a safe evaluation unit, incremental encoders can be used to implement safety functions as required by the IEC 61800-5-2 standard. Safety encoders can be used for an extremely wide range of applications in factory and logistics automation. In the case of stationary machines, mechanical measures such as doors often separate the user from the hazardous point. When carrying out maintenance, safe speed monitoring reduces the risk of injury by slowing down the machine, which allows the operator to manually intervene in the hazardous area. Depending on the field of application, SICK safety encoders can be installed as face mount or servo flange, and blind or through hollow shaft.
Wire draw encoder
Wire draw encoders are a combination of wire draw mechanism and encoder. They record the drum rotation, which is proportional to the length, and provide the corresponding data. This enables positioning on linear measurement paths. Wire draw encoders from SICK have a wide interface selection and enable simple system integration for applications in challenging industrial environments. Goods are often transported across several levels in logistical processes, for example in the automotive industry. Lifts are used for this purpose, and their platforms must be accurately positioned flush to the target level. This positioning is primarily carried out with wire draw encoders.
Linear encoder
Linear encoders comprise one sensor, which serves as a read head, and the reference scale. They determine positions in a wear-free manner due to their non-contact principle of operation. Compact systems with high resolutions or rugged solutions with high measuring lengths (up to 1,700 m) cover a wide range of applications. Cranes are used in almost all areas of logistics. Linear encoders position the trolley on the crane and position the track system of the crane itself.
Measuring wheel encoder
Measuring wheel systems use a wheel to record linear movements and convert them to speed or position values. When used with printing machines, for example, measuring wheel encoders detect the speed of the print media and provide key information on the correct position for the print and the quality of the printed image. The accuracy of the speed recording determines the print quality.
Inclination sensors
Inclination sensors are used to level and monitor the position of objects. They take a non-contact measurement of the inclination angle of an object in relation to the earth's gravity, particularly in off-road use. The inclination angle can be adjusted and the process flow can be effectively designed for different types of terrain. The fast adaptation of the machine to the arable land is essential for harvesting machines, as an example. Inclination sensors are built to be particularly rugged, as they must often withstand harsh environmental conditions.
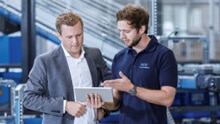