TGW Logistics has gained more flexibility in every respect by using the Safe Entry Exit safety system from SICK. In addition to reliably distinguishing between people and material, this also helps to alleviate space problems in tight plant layouts without additional muting sensors.
Smart intralogistics without muting sensors
If you ask Tobias Czempinski, Director of R&D Smart Robotics & Technical Lead at TGW Robotics, why he wants to mostly do away with muting sensors in the future, you get a clear plea for the use of smart intralogistics solutions: "We were constantly on the lookout for a system that could handle the safety requirements using software. Although we have been working in the Siemens safety world for a long time, the mounting, alignment and reading in of the muting sensors was still a big task. We wanted to move the functionality to where we have to deal with it anyway, which is in the software.” TGW-Robotics, based in Stephanskirchen in Upper Bavaria, is a wholly owned subsidiary of the Austrian TGW Logistics Group. As specialists for robotics applications connected to logistics processes, the automation engineers relied on AI, algorithms, self-teach systems and automated error handling.
Saving hardware – gaining security, transparency and time
With this in mind, TGW customer Heinrichsthaler Milchwerke in Radeberg also installed an automated central palletizing system for cheese products. This is directly connected to the production processes and has doubled output to 100 pallets per hour. At the repalletizing station, the TGW gantry robots are equipped with the Safe Entry Exit solution from SICK for safe human-machine collaboration behind grids. In this case, an existing process signal that cannot be easily manipulated is used to initiate the muting function. As soon as the transport goods have passed the protective device, it is immediately ready again to protect humans from hazards. The control simultaneously evaluates multiple material gates and provides the relevant diagnostic data for Industry 4.0 applications. Tobias Czempinski greatly appreciates the fact that this safety concept works without the usual muting arms: "What we liked about the concept from the very beginning was that you can save on the entire hardware, i.e. the muting sensors. This is not just about the costs, but also about the considerable time saved by eliminating mechanical mounting. After all, cabling and adjustment can become a problem for the commissioning engineers at the construction site if things get more complicated in practice than expected in theory.”
Furthermore, from a control point of view, this solution saves on additional binary inputs and thus lowers costs: This means saving two safe inputs with cross muting and four safe inputs with sequential muting. "This adds up in large facilities like the Heinrichsthaler plant with eight palletizing lines and a throughput of 40,000 cartons per day," Tobias Czempinski emphasizes.
Planning production and distribution centers: The more compact, the better
When designing extensive production and distribution centers, planners focus on creating layouts that are as compact as possible. This often means that the space necessary for the safety technology is lacking. For Tobias Czempinski, one thing is clear: "Every half meter needed for additional photoelectric sensors is hotly contested. We have a lot of machines that work with the inline principle, and for muting sensors we would theoretically need an additional half meter each in the infeed and outfeed. With usually ten lines and thus ten palletizing machines next to each other in the hall layout, the need for conveying lines increases tenfold. That's why our customers and also our colleagues at the TGW Group are very interested in the sensor-free muting solution from SICK.”
More flexible than comparable solutions on the market
TGW has been using various safety photoelectric sensors from SICK's extensive product range for a long time. Lothar Kielwein, Key Account Manager of Intralogistics at SICK, knows that his customer appreciates long-term continuity in the selection of products and explains the great advantage of Safe Entry Exit: "With the new solution, TGW can continue to use the complete selection of safety photoelectric sensors that all employees already know and that have proven themselves in practice. This applies to any type 4 electro-sensitive protective equipment (ESPE), regardless of the beam separation, the scanning range, the resolution: The flexibility remains completely intact. There is no need to purchase a special light curtain that is trimmed for muting.”
Tobias Czempinski is impressed with these advantages: "We also use light grids without muting and can continue to draw from the same product family. This simplifies the processes, because we don't have to worry about storage and various functionalities if we have a total of 28 light grids in use, like at Heinrichthaler.”
Safety certificate reduces documentation work
Given these dimensions, time and cost savings also come into play for documentation and validation. Magnus Utz, Strategic Product Manager at SICK, refers to the certification of the new safety system: "The function block for the safe Siemens S7 control offers a TÜV-certified alternative to classic muting solutions up to SILCL3 and PL e. This means we can efficiently support overall plant validation with a certified system solution.”
Even higher level of safety
"We are once again taking a safe step down the path toward Industry 4.0," says Tobias Czempinski, summing up his experience with the sensor-free muting solution from SICK. "We implement safety solutions because we have to protect the hazardous area of our machines in the best possible way in our daily collaboration with people. Since with the Safe Entry Exit system, we predefine the conveyor speeds and material lengths, it is practically no longer possible to manipulate a safety light barrier or to outsmart it, as sometimes happened in everyday operation with classic muting.”
Following the positive experiences from the Heinrichsthaler Milchwerke project, TGW Robotics has already deployed the sensor-free muting solution in six other plants in a wide range of industries, from fashion and textiles to food, industrial and consumer goods. Feedback on the efficiency and reliability of Safe Entry Exit has been positive without exception.
Muting
Muting describes the safe, automated and temporary bridging of an electro-sensitive protective device during operation. This makes it easy to safely feed material into a hazardous area and then safely remove it.
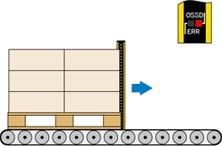
A manipulation-proof process signal, which is typically already available in every plant, is used as the first trigger signal according to the requirement of max. 200 mm in front of the protective device (distance may vary based on the risk assessment).
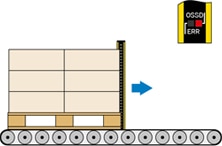
The safe switching signal of the protective device initiates the muting function as the second signal.
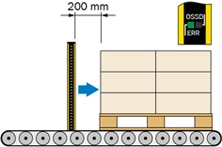
The muting function is terminated no more than 200 mm after leaving the protective field (may vary based on the risk assessment) and the safeguarding of the machine is active again.
Read more